Мировой опыт малой энергетики и когенерации
Предпосылки
внедрения когенерации на молокоперерабатывающих предприятиях
Молокоперерабатывающие предприятия
расположены практически по всей территории Украины, что
обусловлено наличием соответствующей сырьевой базы. В последние
годы прошел период бурного роста объемов производства и
объединения молочных предприятий в холдинговые структуры. В
конкурентной борьбе за потребителя на первый план наряду с
необходимостью технической реконструкции, внедрением европейских
стандартов контроля качества, разработкой новых видов продуктов,
вышли проблемы снижения себестоимости продукции и в первую
очередь – экономия топлива, электроэнергии, воды, улучшение
очистки сточных вод. Важнейшая задача сегодня - это серьезная
реконструкция производства, основанная на новейших технологиях и
процессах, предлагающих существенные возможности экономии
энергии.
Для молочной промышленности характерно то, что электрическая и
тепловая энергия потребляются одновременно. При этом
электроэнергию получают от сетей энергоснабжающих компаний, а
тепловая энергия - производится собственными котельными.
Практически отсутствующая на данный момент конкуренция среди
генерирующих и энергораспределительных компаний приводит к
отсутствию мотивации в сокращении издержек при производстве,
транспортировке и поставке электроэнергии конечным потребителям,
вызывает постоянный рост цен на энергоносители для конечных
потребителей и негативно сказывается на себестоимости продукции.
Удельное потребление энергии (количество использованной энергии
на производство одной тонны переработанного молока) отличается в
значительной степени среди различных предприятий и зависит от
ассортимента продукции, загруженности предприятия, эффективности
используемого оборудования и его технического состояния. В
производственных затратах молокозаводов в Украине расходы на
энергоресурсы составляет 10%, а в странах-членах ЕС всего
0,8-2%.
Для существенного снижения энергоемкости и, соответственно,
себестоимости молочной продукции необходима альтернативная более
эффективная технология энергоснабжения. В настоящее время самой
эффективной технологией производства электрической и тепловой
энергии из органического топлива является когенерация и
тригенерация. Когенерационные установки на базе газопоршневых
двигателей имеют наивысшую на сегодняшний день эффективность
преобразования энергии топлива в электричество. Например, для
современных установок производства General Electric GE Jenbacher
(мировой лидер в производстве газопоршневых двигателей и
электростанций на их базе), электрический КПД составляет 43%, а
с учетом тепла общий КПД достигает 90%. Это позволяет иметь
минимальную топливную составляющую в себестоимости производимой
электроэнергии.
Суть нового подхода к энергообеспечению молокоперерабатывающих
предприятий – использование когенерационных технологий и
технологий тригенерации для собственной комбинированной
выработки дешевой электроэнергии, тепловой энергии при сжигании
природного газа с максимальной эффективностью в когенерационных
газопоршневых установках и преобразование последней в
холодоноситель для использования в технологических
производственных процессах молокозавода.
На молочных предприятиях холод используется в технологических
процессах производства продукции, для хранения продукции, а на
сырзаводах – еще и для камер созревания сыра. Технические
особенности абсорбционных чиллеров позволяют получать лед-воду с
температурой 5-10 оС, поэтому для камер хранения продукции
целесообразно использовать компрессионную холодильную технику, а
потребности в холоде (лед-воде) технологических процессов можно
обеспечить абсорбционными чиллерами, работающими в комплексе с
когенерационными модулями.
Применение для молочных предприятий тригенерационных комплексов
в составе собственных мини-ТЭЦ и абсорбционных холодильных машин
решит известные сегодняшние проблемы, приведя электро-, тепло- и
холодоснабжение к современному техническому уровню, снизит
затраты на энергоресурсы, обеспечит независимость производства
от внешних сетей облэнерго
Конкретные и неоспоримые конкурентные преимущества собственной
когенерационной электростанции:
* Более эффективное использовать сжигаемое дорогостоящее топливо
(общий КПД использования топлива в установках достигает 90%);
* Возможность получения дешевой электроэнергии для нужд
потребителей молокозавода;
* Получение необходимого количества дешевого теплоносителя для
технологии тригенерации;
* Снижение уровня выбросов вредных веществ и парниковых газов;
* Внедрение передовой высокоэффективную технологию тригенерации
в технологический цикл предприятий.
Традиционное электроснабжение молокоперерабатывающих предприятий
осуществляется от сети облэнерго по 33,7 коп/кВтч (без НДС) -
тариф 2-класса (напряжение ниже 35 кВ). При сегодняшней цене
газа на собственной ТЭЦ на базе модуля GE типа JMC-420 мощностью
1,4 МВт (электрической) и 1,4 МВт (тепловой) затраты составляют
до 18 коп. за 1 кВтч электроэнергии и еще 1 кВтч тепловой
энергии без дополнительных затрат. С учетом замещения
производства тепла на существующей котельной тепловой энергией
от когенерационных модулей: себестоимость электроэнергии 11
коп/кВтч, а себестоимость тепла – до 80 грн/Гкал.
При увеличении цены газа например до 260$, себестоимость
выработки электроэнергии на собственной ТЭЦ, с учетом
производства тепла, составит 16,7 коп/кВтч., что все равно
намного выгодней, чем покупать в облэнерго. Но удвоение цены на
газ пройдет на фоне увеличения цены и на электроэнергию. Есть
много объективных факторов для роста цены на электроэнергию: тот
же рост цен на топливо, в т.ч. природный газ, уголь и ядерное
топливо, необходимость обновления распределительных сетей и
генерирующих мощностей, рост заработной платы персонала по всей
энергетической отрасли (от шахтеров до обслуживающего персонала
тепловых электростанций и распределительных сетей) и т.д.
Благодаря такой экономии затрат простой срок окупаемости проекта
по строительству собственной ТЭЦ может составить 3 года при
правильном выборе генерирующего оборудования и режимов его
работы.
Внедрение когенерации можно проводить параллельно с внедрением
3-х зонного учета. Тогда Собственник получает возможность
дополнительно снизить затраты на энергоснабжение, получая
электроэнергию от сетей облэнерго по дешевому ночному тарифу, а
в периоды дорогой пиковой и полупиковой электроэнергии
производить электричество на собственной когенерационной
электростанции.
В начале 2007 года действует такой коэффициент к одноставочному
тарифу в период ночного провала нагрузки (7 часов) k = 0.25.
Таким образом, цена электроэнергии в ночной период будет дешевле
себестоимости ее производства. Отключая когенерационные
установки на ночной период Собственник может снизить затраты на
энергоснабжение еще на 10÷30% (по сравнению с постоянной работой
когенерационной станции). По такой схеме работает большинство
маневренных электростанций в Европе.
Одним из важнейших преимуществ внедрения когенерации является
повышение надежности энергоснабжения. Цена надежного
электроснабжения достаточно высока: отсутствие, или внезапное
отключение энергоснабжения несет за собой недополучение прибыли,
а возможно убытки и потерю деловой репутации. Аварийные
отключения могут стать причиной выхода из строя дорогостоящего
оборудования, потерь сырья и порчи продукции.
В случае наличия собственной ТЭЦ потребитель застрахован от
перебоев в централизованном энергоснабжении, время от времени
возникающих либо вследствие износа основных фондов
энергоснабжающих компаний, либо других непредвиденных причин.
Помимо этого, устраняются организационные, финансовые и
технические проблемы при реконструкции и росте мощностей
предприятий, поскольку не требуется прокладка новых линий
электропередач, строительство новых трансформаторных подстанций,
перекладка теплотрасс. Кроме того, Собственник защищен от
монопольного повышения тарифов на энергоснабжение.
Особенности конструкции, выбора и инсталляции когенерационных
установок на предприятии
Когенерационные модульные установки хорошо вписываются в
существующую инфраструктуру предприятия. Возможны два варианта
размещения:
1) Исполнение во всепогодном, шумозащитном кожухе комплектной
поставки открыто на фундаментах возле здания существующей
котельной. Когенерационный агрегат в контейнерном исполнении
представляет собой полностью смонтированный производителем
функциональный модуль, в состав которого входит как основное
оборудование, так и такие вспомогательное системы как масляное
хозяйство, вентиляция, пожарная и газовая сигнализации. Может
быть в сжатые сроки установлен и, после подключения инженерных
коммуникаций, запущен в эксплуатацию.
2) Открытое исполнение для установки в существующем здании
котельной.
Когенерационный модуль представляет собой агрегат, в состав
которого входят:
1. Четырехтактный газовый двигатель с искровым зажиганием,
турбонаддувом газовоздушной смеси, оснащенный специальной
системой управления.
2. Электрогенератор.
3. Теплообменники: масла, 1-ой ступени газовоздушной смеси,
рубашки двигателя, тепловая мощность которых используется для
подогрева теплоносителя (вода 90/80°С). Дальнейший подогрев
теплоносителя производится в теплообменнике выхлопных газов. В
теплообменнике 2-ой ступени газовоздушной смеси отбирается
низкопотенциальное тепло, которое выбрасывается в атмосферу
посредством вентиляторного охладителя.
Источником теплоснабжения являются агрегаты (модули),
предусматривающие использование тепловой энергии в виде горячей
воды 110/70 °С, либо пара. Вырабатываемая вода с температурой
110 °С используется абсорбционными холодильными машинами для
производства холода (лед-воды).
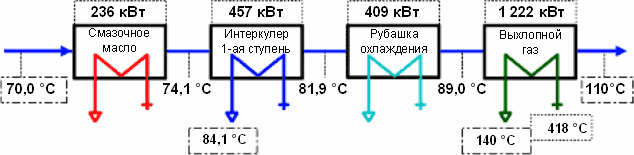
Рис.1. Тепловая принципиальная схема
выработки воды с температурой 110 °С.
При снижении потребления горячей
воды абсорбционными холодильными машинами, излишнее тепло
утилизируется системой аварийного охлаждения сетевой воды.
Система аварийного охлаждения обеспечивает нормальную работу
агрегатов при полном отсутствии присоединенной нагрузки
теплоснабжения.
На молокоперерабатывающем предприятии использование когенерации
позволит исключить из себестоимости продукции затраты на закупку
электроэнергии. Обеспечивается сокращение расхода газа на
котельной в следствие использование горячей воды, для промывки
оборудования и технологических трубопроводов и отопления от
собственной мини-ТЭЦ.
Кроме того, снижаются объемы потребления собственной
электроэнергии на производство холода (лед-воды) для
технологических нужд. Благодаря использованию абсорбционных
чиллеров повышается холодопроизводительность холодильной
установки при снижении потребляемой электрической мощности,
используются хладагенты R-134a, R-718 (вода), без применения
аммиака в системе.
Молокоперерабатывающие предприятия в Украине, где уже работают
когенерационные установки: молокозавод «Рогань» г. Харьков (1
МВт эл.), предприятие «Фани» г. Павлоград Днепропетровской
области (0,5 МВт), разработан проект с использованием
тригенерации для Донецкого молзавода и еще целого ряда
украинских молочных заводов и сыркомбинатов.
Еще одним важнейшим применением когенерационной установки на
молокоперерабатывающих предприятиях является использование тепла
выхлопных газов газопоршневого двигателя в процессах сушки
сконцентрированного цельного молока, сконцентрированного
обезжиренного молока, заменителей цельного молока с содержанием
жира 30%, а также сконцентрированной подсырной сыровотки – в
качестве альтернативы для паровых систем и теплообменников
пар-воздух.
Цеха сушки потребляют в среднем 60 % всего пара, вырабатываемого
котельной, причем давление пара требуется 11-12 кгс/см2. Как
правило, цеха сушки находятся на значительном расстоянии от
котельных, а на многих предприятиях неудовлетворительное
состояние изоляции паропроводов, что приводит к потерям.
Оснащение цехов сушки молока когенерационными установками
позволит существенно разгрузить существующие котельные.
Тепловая мощность, которую можно получить от выхлопного газа
зависит от установленной мощности когенерационного модуля,
например: до 0,44 МВт – от модуля в 1 МВт установленной
мощности, 1,4 МВт – от модуля 3 МВт. Температура выхлопных газов
газопоршневого двигателя достигает 500 оС. Объем выхлопного
газа: 4491 нм³/час (модуль 1 МВт), 13 666 нм³/час (модуль 3
МВт). В качестве сушильного агента применяется воздух. Его
нагрев может быть произведен путем подачи воздуха в сушильную
камеру через воздухоподогреватель за счет утилизации тепла
отходящих продуктов сгорания. Воздухоподогреватель располагают
по ходу движения продуктов сгорания. Обычно для нужд сушки
воздухоподогреватели рассчитываются на заданную
производительность по горячему воздуху с температурой 200 °С.
Использование когенерации выгодно и в случае, если в цехах сушки
вместо паровых калориферов уже были установлены газовые
теплогенераторы. Когенерационный модуль кроме такого же
продукта, как и у теплогенератора, - горячего воздуха, еще
обеспечивает производство электроэенргии.
Очевидно, что при реализации проектов когенерации на украинских
предприятиях в будущем ставку нужно делать на выбор
когенерационного оборудования, имеющего максимальную
эффективность.
Экономически целесообразно применять оборудование, которое
характеризуется минимальным потреблением топлива, при этом, в
первую очередь, с высокой эффективностью производить
электрическую энергию, как самый дорогой продукт, т.е. иметь
максимальный электрический коэффициент полезного действия (КПД).
При этом тепловая энергия производится путем утилизации тепла от
работающего оборудования во время производства электроэнергии.
Электрический КПД современных когенерационных установок
достигает более 43 %, при этом на каждый 1 кВт*час полученной
электроэнергии производится 1 кВт*час полезно используемой
тепловой энергии.
Очистка сточных вод молокозаводов и сыркомбинатов с получением
биогаза и его утилизацией в когенерационных установках с
выработкой электрической и тепловой энергии.
В последние годы в Украине наблюдается процесс технического
перевооружения молокоперерабатывающих предприятий. В первую
очередь это касается процессов производства: предприятия
закупают новые технологические линии, разрабатываются и
запускаются в производство новые продукты (творожно-сырковая
продукция, молочные десерты, йогурты, и т. д.). Изменение
технологии влечет за собой изменение качества образующихся
сточных вод. Кроме того, все большее внимание уделяется
рациональному потреблению свежей воды. Снижение ее потребления
приводит к тому, что сточные воды молокозаводов становятся более
концентрированными при уменьшении их общего количества. Для
многих предприятий соответствующая очистка сточных вод
представляет серьезную проблему.
Это происходит на фоне возрастающего давления на предприятия со
стороны водоканалов и контролирующих органов. Все чаще перед
предприятиями встают проблемы поиска эффективных, надежных в
эксплуатации, гарантирующих стабильное и высокое качество
очистки очистных сооружений, а во многих случаях – реконструкции
и расширения уже имеющихся. Рост стоимости
топливно-энергетических ресурсов заставляет украинских
производителей задуматься и о таких источниках снижения
себестоимости молочной продукции, как рациональное использование
энергоресурсов, эффективное управление отходами производства,
одним из которых является сточные воды.
Многие предприятия пытаются оттянуть момент, когда придется
заняться очистными сооружениями, считая это высокозатратным
мероприятием, которое не принесет ни какой пользы
непосредственно производителю молочной продукции.
Решение этой проблемы – выбор наиболее эффективной,
энергосберегающей технологии очистки сточных вод
молокоперерабатывающих предприятий с получением биогаза и
дальнейшей его утилизации в когенерационных установках с
получением электроэнергии и тепловой энергии. Кроме того, на
многих молокоперерабатывающих предприятиях, которые производят
твердые сыры, образуется большие количества подсырной сыворотки,
которая практически не пригодна для дальнейшей переработки, и с
утилизацией которой многие предприятия имеют серьезные проблемы.
Эта сыворотка может с успехом использоваться для производства
биогаза.
Метановое брожение используется как предварительная стадия
очистки концентрированных стоков с последующей аэробной
доочисткой. При этом образуется большое количество биогаза, с
содержанием метана до 60-80 %.
Вода, очищенная на 60-80% с применением анаэробного метода,
направляется на существующую аэробную доочистку в аэротенк, где
достигается требуемая степень ее очистки.
Метанреакторы позволяют получать на выходе сточную воду с БПК –
100-300 мг О2/л, выход биогаза составляет 0,6 л/кг ХПК. Степень
очистки по ХПК, БПК достигает 80-95%, по взвешенным веществам
более 85%.
При концентрации загрязнений на входе (по ХПК) 2000 – 20000 мг/л
сбраживающая мощность реактора достигает (по ХПК) 10-40 кг/м3/сут,
время пребывания сточной воды в реакторе 20-30 ч. Процесс
метанообразования практически сразу откликается на изменение
нагрузки на реактор, при пиковых нагрузках на очистные
сооружения и после кратковременных перерывов в подаче сточной
воды.
Затраты электроэнергии на 1 кг удаленных загрязнений (по ХПК)
для анаэробно-аэробного процесса составляют 0,2-0,4 кВт.ч/кг ХПК,
что также в десять и более раз ниже показателей, типичных для
аэробных процессов. При этом количество образуемого избыточного
ила (сумма анаэробного и аэробного) составляет 0,14-0,18 кг/кг
ХПК (по абсолютно сухим веществам), что в 2-3 раза меньше, чем в
случае использования только аэробного процесса.
Как показал опыт молочных заводов, применение современных
анаэробных реакторов для очистки сточных вод позволяет решить
сразу несколько проблем: обеспечить высокую производительность
очистных сооружений, повысить качество очистки сточной воды,
резко уменьшить количество избыточного ила и за счет
использования образующегося на предприятии биогаза снизить
потребление покупного газа. При этом локальные установки для
удаления жира и взвешенных веществ из сточной воды не нужны.
Наоборот, концентрированные загрязнения – жиры, белки, углеводы
должны быть направлены непосредственно и без потерь на
биологическую очистку и подвергнуты биоконверсии для получения
максимального количества биогаза.
Технологии GE Jenbacher дают возможность использования биогазов,
газов сточных вод, мусорных свалок, пиролизных, синтез-газов и
других особых газов для получения электроэнергии и тепловой
энергии. Постоянное совершенствование двигателей GE Jenbacher и
специализация на использование особых газов обеспечивают
возможность применения газов с низкой теплотой сгорания.
Примеры молокоперерабатывающих предприятий, где внедрены
технологии получения биогаза:
Молокозавод MILCHWERKE DONAUALB (Германия). Переработка -
490-500 т. молока в сутки, Ассортимент продукции включает в себя
различные виды сыров и масло. Кислотная казеиновая сыворотка
проходит ультрафильтрацию. Концентрат с высоким содержанием
белка используется повторно. Раствор, состоящий из лактозы, соли
(воды 94%), ранее сгущался в отстойнике до содержания сухого
вещества (35%), после чего он сбрасывается в канализацию.
По новой технологии концентрат предварительно подогревается и
подается в два анаэробных ректора, объемом 2000 м3, в которых
вырабатывается биогаз. Скорость подачи составляет 250-300
м3/день с продолжительностью выдержки 10-12 дней. Содержание
метана в получаемом газе составляет около 65% с теплотворной
способностью примерно 6,6 кВт*ч/м3. Количества вырабатываемого
биогаза хватает на использование использовать в качестве топлива
для установки комбинированной выработки тепловой и электрической
энергии мощностью 500 кВт.
Осадок представляет собой безвредное вещество, пригодное для
использования в качестве удобрения. Стоки, прошедшие
предварительную очистку, направляются на водоочистную установку
для дальнейшей очистки.
Общие капиталовложения на установку получения биогаза составляют
до 3 млн. евро, включая стоимость блочной установки
комбинированной выработки тепловой и электрической энергии.
Годовая экономия: электроэнергия 3600000 кВт*ч, воды 15000 м3
Срок окупаемости 3-4 года. При этом, произведенная энергия
позволит окупить расходы на установку комбинированной выработки.
Молокоперерабатывающее предприятие Наабталер Мильхверк
Бехтель ОХГ (г. Шварценфельд, Германия).
Количество сточных вод, образующихся при производстве сыров и
молочных продуктов, до 1100 м³ в сутки Объем метанреактора 900
м³ Выход биогаза 2000 м³ в сут.
Молокоперерабатывающий завод "Ehrmann", Москва,
Молокоперерабатывающее предприятие "Norrmejerier", Швеция
(проект по переработке сыворотки с целью получения биогаза).
Иванько А.А., руководитель проектов ЧНПП «СИНАПС», май 2007 г. |